Müller Martini Boosts Efficiency With Integrated FSM
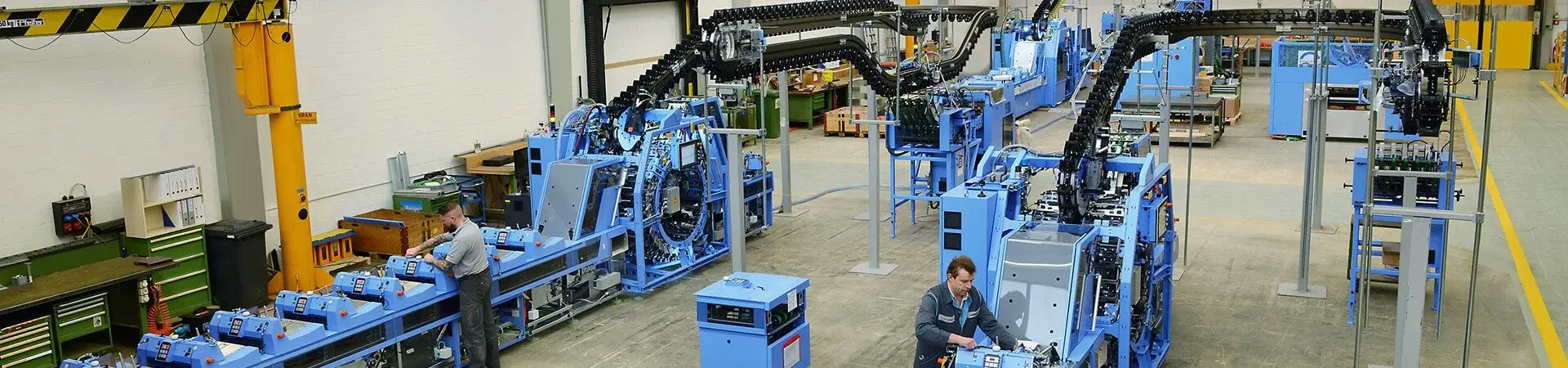
Initial Situation
Since the paper finishing sector was not showing any growth potential over time, Müller Martini decided to adjust its business concept in 2014. During the course of a restructuring project of the global distribution and service organization, profitability was to be improved and processes expedited in order to establish the company as a top print industry provider in the after sales services sector - a concrete USP that would lead to an increase in new long-term investments. To lay the groundwork for this restructuring, Müller Martini needed an IT concept that facilitated continuous processes while also connecting all locations.
Non-uniform Processes Slowed Workflows
In the past, Müller Martini was positioned as a closed unit at its Swiss head office. The distribution company worked closely with production and development. However, for the most part the international distribution branches used completely different systems that lacked uniform processes. Even the company’s own production facilities in Germany were not connected to the solution at the Swiss head office.
Solution
Müller Martini opted for a combination of SAP Business One, SAP ECC as its ERP basis, and the Coresystems FSM solution. A connector in between exchanges data between the cloud application and on-premise systems. With the help of intercompany interfaces between SAP Business One and SAP ECC, data is transferred between applications and core data between production and distribution companies is synchronized. This is how all locations are mapped using three systems.
Improved Profitability and Transparency
By departing from a wide variety of applications, worldwide company processes could be standardized, simplified, and automated. There was also an increase in transparency since information is only in one system. Key figures can also be collected and data evaluations initiated with one and the same tool. The result is uniform data quality that makes financial planning easier.
The integrated solution made up of ERP, CRM, and FSM offer a highly-effective and user-friendly connection of the distribution and service sectors to the main company software. It is the connection of the FSM solution in particular that makes it possible to manage service calls reliably while conserving resources, and provides the option to quickly enter sales CRM data. - Reto Hofer, Program Manager MMServices, Gobal Services and Marketing
Focus on Service Reinforces the Role of Technical Experts
The technicians are a special feature: the specialists are associated with the production facilities in Switzerland and Germany. If necessary, orders from local technicians can be forwarded to specialists using the solution implemented by Coresystems. They can use the system to view and process integrated data. As soon as the problem has been resolved, orders can be completed within the system and transferred back to the local technician.
About Müller Martini
Müller Martini AG, located in Zofingen, is an internationally operating, independent, family-owned company and global leader in the development, production, and marketing of print finishing systems. As part of its Finishing 4.0 development strategy, the company offers innovative solutions for the finishing of digital and offset printing. With over 20 sales and service companies, 40 agencies and production sites in Switzerland, Germany, the USA and China, the company can quickly be on site on any continent. The Group employees around 2400 employees worldwide.